We currently use a gas-fired kiln that we built about 10 years ago. We have fired a lot of pottery in this kiln over the years, and in many ways it has worked well for us, but it has a fundamental design flaw that makes the kiln very difficult to use, especially with certain types of glazes.
Types of Kilns
There are two basic types of fuel fired kilns: natural draft kilns, and forced air kilns. A natural draft kiln uses the draft produced by the chimney to pull air into and through the kiln, and dampers are used to regulate the atmosphere within the kiln. A forced air kiln, such as ours, uses fans to blow the flame from the kiln’s burners into the firing compartment where the pottery is located. This type of kiln doesn’t need any secondary draft, such as that produced by the chimney, and in fact any secondary draft makes the atmosphere inside the kiln difficult to regulate.
The Problem with our Existing Kiln
The chimney on our kiln is too large in proportion to the rest of the kiln. Because of this, it produces some secondary draft, which causes turbulence. The draft also makes it hard (or impossible, depending on weather conditions) to regulate the atmosphere inside the kiln.
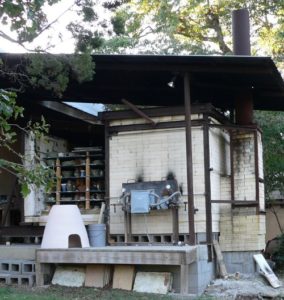
When firing pottery, one very important stage in the process is the reduction stage, in which firing temperatures are in the 1,600 to 1,900 degree range (Fahrenheit), and the air intake is adjusted to reduce the amount of oxygen in the firing chamber. This “oxygen poor” environment draws out oxygen that is stored in the chemical makeup of the glazes. This causes the glazes to change to the proper colors.
If there is too much oxygen in the air, the glazes will not change color properly, and if there is too little oxygen, the fire will become sooty, producing a lot of carbon, which also interferes with the glazes. It is important to get just the right oxygen content, and that is what we are unable to do with this kiln.
Red Glazes Turn White
This has been most apparent when we have used red glazes. If the oxygen level is incorrect during the reduction phase, the red pieces turn white. Sometimes the whole piece turns white. Other times, part of the piece will turn white. Once the piece has been fired, certain minerals in the glazes have been vaporized, and re-firing the piece will not correct the problem. We no longer fire red pieces in this kiln because it is impossible to fire them reliably. In the photo below, both pieces of pottery were glazed with a red glaze, but due to the incorrect atmosphere in the kiln, the pot on the left turned white. The piece on the right turned red in most places, but turned white near the rim. Although the glaze color does not affect the usefulness of a piece of pottery, it does make the piece unsalable when part of a custom order.
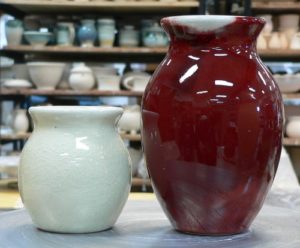
Our signature Homestead Green pottery also is difficult to fire in this kiln. The effect is less pronounced than for the red pieces, but still very noticeable. Normally, the glazes produce a beautiful translucent, opalescent finish, but when the kiln’s atmosphere is incorrect, the finish becomes metallic green.
A Sustainable Wood-Fired Kiln
Because of these problems, we plan to begin building a new wood-fired kiln very soon. It will be a double fast fired kiln and will use only renewable resources (wood, which is plentiful here). It will require no electricity to operate. We are working toward sustainability in our community, and this kiln will take us another step toward developing a sustainable pottery shop and teaching facility.
We’ve discussed the kiln design with a number of other experienced potters, and we feel that this particular design is the best suited to our needs. There are several types of wood kilns, but this particular type will let us produce pottery that is very similar to the pottery that we currently fire in our gas kiln.
Once we have built the new kiln, we plan to operate it alongside our existing gas kiln until we have gained enough experience with it. Then we plan to dismantle the gas kiln and build a second wood kiln using its materials.
The wood fired kiln will cost about $5,000 to build and will contain more than 1,500 fire bricks.
Update 5/21/2012
We have nearly completed the kiln. See this update on the kiln for more information.